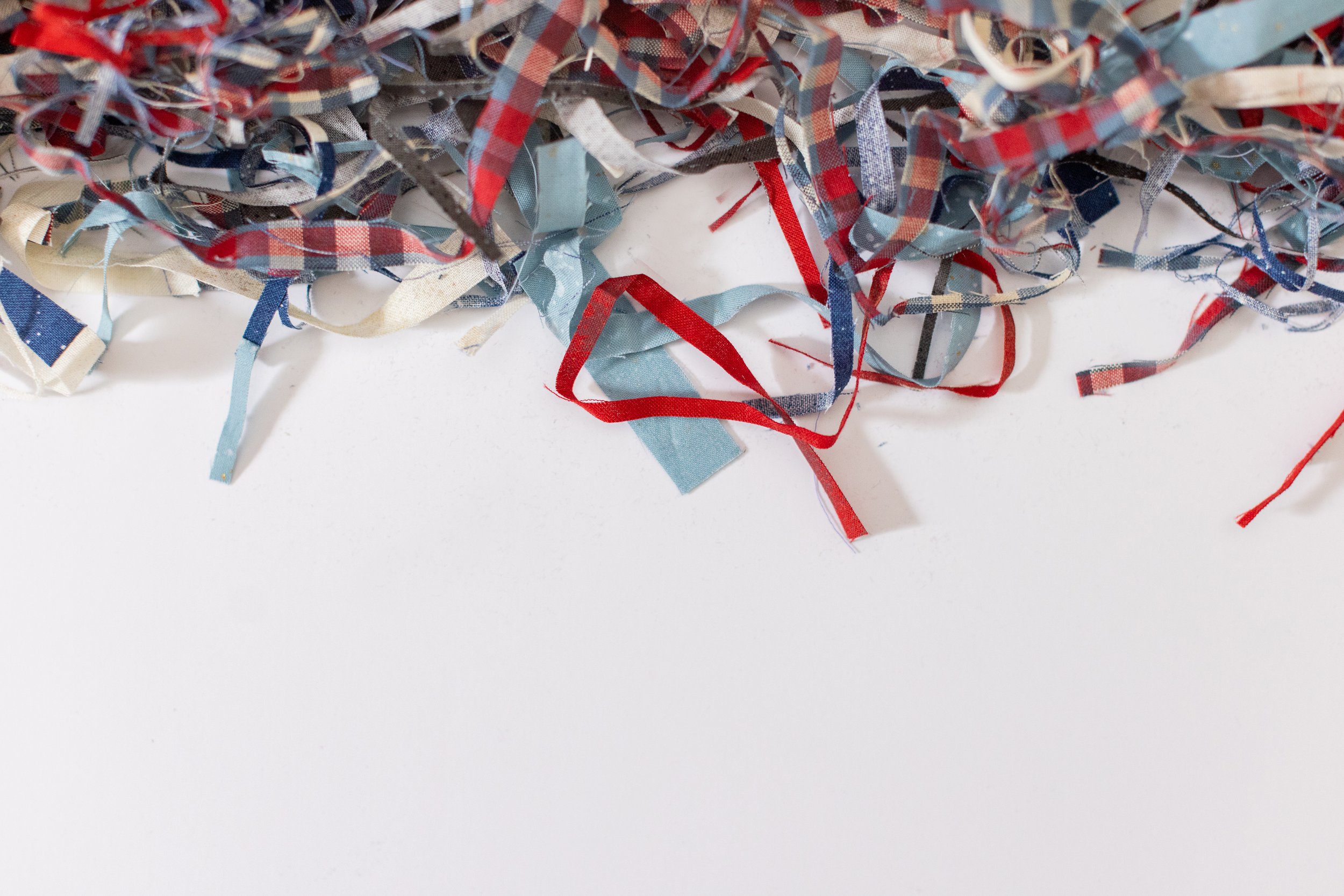
General Frequently Asked Questions
-
There are so, so many things one could tell you about the longarming world. Much of it is helpful, easy, and quick. But there is quite a bit that is nuanced and somewhat difficult to explain. Some of it you NEED to know, some of it only applies in some circumstances, and some of it is absolutely unhelpful and unnecessary. In an effort to both organize and prioritize all of this information, we have this general FAQ page to cover all the basics, a Backing Information page to address all things backing related, and a Pantograph Information page to cover info on our quilting patterns. If you can’t find an answer in one of those three places, contact us and we will be happy to help!
-
We have a few tabs of info if you scroll down just a bit on this page to cover the very basics. However, there are so many things to cover with backings we’ve developed an entire Backing Info page. Check it out for alllll the info you will find helpful!
-
We’ve covered everything we can think of in relation to your backing on our Pantograph Info page. Within those topics we occasionally have fleshed out more details in our blog. Links to each of these detailed topics will be linked within their perspective expansion area.
You can find all our current pantograph offerings here!
-
I recommend starting with either the Longarm Quilting Services page or the order form. Both of these have the most updated pricing and information to get you started. Both give a brief, but helpful, guide to how to prep your top and back, what we offer, and how to get your quilt to us.
If you continue to have questions then the various FAQ and information pages should be helpful, and you can always reach out directly to us.
-
We do have a minimum charge of $50 on the quilting services for any one project. This charge applies regardless of any discounts, coupons or other price reducing deals we may be running. Regardless of size, it takes time to prep, communicate with the customer, load the quilt, prep the thread, trim, and invoice. This minimum charge helps us balance these tasks with the smaller quilts that come through the studio.
There are a couple of ways around this minimum. If you are quilting two things with the same pantograph, thread color, and backing fabric, it’s possible to quilt both items at the same time. Simply make your backing large enough for both (pay attention to orientation of your projects and the panto!). This can work well for baby quilts and larger quilts with matching pillowcases or table runners. I encourage you to reach out if you want to try this to make sure we are on the same page as to how this works.
-
We are very chill longarmers and will happily work with just about anything you send us. However, the better you prep your quilt top, the better our results will be and the happier you will be with the finished product. You’ve already spend lots of time and money on your quilt, let’s get you set up for success! The next couple of drop downs will outline our recommendations.
-
Pressing your quilt top is the most important thing you can do to prevent weirdness from happening. When we talk about pressing, it’s mostly about getting your seams, points, and corners as flat as possible without the fabric on the front folding over itself.
From the front: press it so your fabric does not overlap itself near the seams and watch for any spots where the seam has come undone leaving a hole.
From the back: press your seams, corners, and points as flat as you can get them. We do not have a preference in regards to pressing seams open, to the sides, or to the dark side. Some longarmers do not care for open seams because if they are doing custom stitch-in-the-ditch work it’s easy to pop those seams leaving a hole. But many pattern writers recommend pressing seams open. It’s a bit of a disconnect but rest assured, TCQ does not have a preference.
Shipping your quilt? It’s true, placing your quilt in a tiny box for a few days may cause a few creases. No worries, this is expected and easily comes undone with once it arrives and hangs up for a few days.
-
Trimming threads is all about preventing dark threads from showing through on lighter fabrics. Beyond that, this step has no effect whatsoever on our quilting process. If you have a navy and white quilt and the navy frays like crazy, you have a lot of work to do. If your quilt is entirely darker fabrics, you don’t have a thing to worry about.
Here at TCQ we do not trim threads. We do understand that no matter how much you trim more thread will appear, it’s the nature of the beast, and we will do our best to keep an eye out for anything that might show through. But beyond that, you are in charge of how much trimming takes place.
-
We have a million things to say about backing fabrics, prep, and nuances on our Backing Information page. I strongly encourage you to check it out if you are thinking about using fabrics other than regular quilting cotton, have backings that do not meet our measurement requirements, and to catch our thoughts on where you seams fall, using panels, centering piecing on the backings, and much much more. And if we don’t have an answer for you, reach out and we might just add it to the page. We are going to cover the basics below, however, so read on!
-
To ensure the best results on your quilt top, your backing fabric needs to be 4” larger than your quilt top on all 4 sides. It’s an easy equation - simply measure your quilt in inches, then add 8” to the width and add 8” to the length. Those will be your minimum backing measurements. Example: for a 60” x 80” top your backing will need to be a minimum of 68” x 88”.
We do not expect your backing to be exactly 8” longer and wider. Please do not stress about trimming everything exactly to size. Your backing can certainly be bigger than this. Bigger is usually better as it gives us extra room to work. Unless you indicate otherwise, we will always return significant scraps to you after trimming.
Returning Significant Scraps: The extra inches we ask for should be considered a part of the quilting process, much like a seam allowance. It may not show on the quilt top, but you wouldn’t expect to trim it off and use it for something else. We evaluate each quilt that comes in and work hard to get you back as much fabric as is reasonably possible.
Why do we ask for extra fabric: We use this extra fabric and space for several things.
1. We pin your backing fabric to our machines.
2. We use side clamps to keep the backing fabric even, taunt, and in place while the machine is quilting.
3. We often do a thread tension check in these margins.
4. Not all machines have the capacity to trim the panto we are running to the same size of the quilt top. In these situations, we need some extra room to run the panto off the quilt top to properly repeat the pattern and avoid any gaps from where the panto nests with itself in each pass.
5. Quilt tops and quilt backings are rarely perfectly square. Having that extra wiggle room is important in case the quilt drifts one way or the other as we work our way down the quilt top. -
It’s pretty clear to me that most folks don’t quite understand what ‘squaring’ means and/or how quilts are loaded onto a longarm. I get it, but let me see if I can educate you a tad bit:
Squaring your backing: First, squaring your backing does not mean it is square. It simply means you have four straight edges that are perpendicular/parallel with each other. I do not need absolute perfection, but it should appear fairly square to the naked eye when laid out flat on the floor.
Common issue: The most common thing we see is when you piece your backing together, and one piece was cut a tad bit larger than the other side. Now that it’s pieced together, that larger piece hangs out wider or longer than the other creating not a straight line, but an uneven edge. While we have ways to maneuver around this, it really ought to be trimmed so that edge is even and straight.
Why you should square your quilt: The first step in loading a quilt on the machine is to pin your backing to our leaders. This provides and determines the stability to the rest of the entire process. If we don’t have something square, with straight lines that are perpendicular and parallel to each other, then we are backfooted from the start. Some common problems from this are droops in the backing fabric, uneven tension, puckers or pinches, and accidents in running out of backing fabric halfway through the quilting process.
-
If your backing has a ‘top’ and a ‘bottom’ orientation, please mark it. Something that may feel obvious to you may not be to us. Particularly fabric that is subtly directional.
Common ways to mark your backing include painters tape and pinned notes or other easily spotted and securely attached methods. Binding clips often slip off in the unpacking and prep process, and lone safety pins are often missed and can become a hazard to the machines and the staff.
-
TCQ is happy to piece your backing for you. Simply send the correct yardage for a backing remembering it should be no less than 8” wider and longer than your quilt top and we will do the rest. We do not have a space for this service on our order form simply because it’s usually fairly obvious that it’s something you need completed and our order form is already pretty packed. :)
We will automatically piece your backing with the least amount of seams possible. If your fabric is directional we will orient it correctly. If you would like for your backing fabric pattern to match, be sure to make a note on the order form as this is not an assumption we will automatically make. You will also want to be sure to order extra fabric to ensure we have enough.
Pricing: $15/seam for basic piecing.
$30/seam to pattern match. -
We are more than happy to help with the binding stage of completing your quilt top. We offer two levels of service: We can attach it to the front for you to turn and and stitch on the back. We can also finish the binding completely by machine stitching in the ditch from the front and catching the binding on the back.
We prefer binding strips that are 2.5”, straight cut, from quilting cottons. You may send the yardage or make the binding completely so it’s ready to attach to the quilt and anywhere in between. There is no difference in pricing, it is a complimentary service to make it our preferred way for you.
Bindings that fall outside of those parameters are often fine though we encourage you to reach out to confirm we can meet your expectations as well as evaluate if it will incur any additional charges. Examples are binding that is smaller or larger than 2.5”, store bought binding, making bias binding for you, etc.
-
To ensure the best results on your quilt top, your batting needs to be 4” larger than your quilt top on all 4 sides. It’s an easy equation - simply measure your quilt in inches, then add 8” to the width and add 8” to the length. Those will be your minimum batting measurements. Example: for a 60” x 80” top your batting will need to be a minimum of 68” x 88”.
I’ll let you in on a little secret: it’s not as imperative to have those 8” as it is for the backing fabric. We are not pinning to it and we can manipulate batting a little easier than backing fabric if we run into trouble. That being said - you should still aim to ensure we have this minimum for the best results on your quilt top.
Please note: We do not return batting scraps unless special arrangements have been made. This extra bulk in our return packing comes at a fairly significant cost. We share and donate significant batting scraps with several groups, local crafters, and organizations so it doesn’t go to waste. We chat a bit about this on our ‘About Us’ page.
-
We currently offer two types of batting at our own wholesale cost for everyone’s convenience. Both options come 96” wide on rolls so there are no wrinkles, creases, or vacuum-packed issues to work through before we can use it in your quilt. About 85% of our customers have us provide the batting for them.
1: 50/50 cotton/bamboo, 96” wide: $3.50/linear foot.
2. 100% wool, 96” wide: $5/linear foot.
Both types come with a king sized option to cover quilts bigger than 96”. They are $45 and $60 respectively.More details:
Our first option is the 50/50 cotton/bamboo batting 96” wide at $3.50/linear foot. Quilts whose smallest measurements exceed 90” will get a king batting package at a flat fee of $45. We use Kyoto by Luna unless otherwise noted. This is a low loft, all natural, sustainable, hypoallergenic, and environmentally friendly option that is supremely soft and has a divine drape. It is a natural color and is by far the most common selection. The manufacturer’s description is as follows:Kyoto is a bamboo and cotton blend. Bamboo is softer than cotton, biodegradable, hypo-allergenic and eco-friendly. Naturally antibacterial. It has been blended with cotton for the perfect natural quilt batting. Cleaned without harsh chemicals. Needle punched to a thin scrim using no binders or resins. Will not shift or shed. Stitch up to 8" apart. Shrinkage is approximately 3% after wash. Made in the USA.
Our second option is 100% wool batting 96” wide at $5/linear foot. Quilts whose smallest measurements exceed 90” will get a king batting package at a flat fee of $60. All natural, super breathable, and with a higher loft, this is a great option to make a warmer quilt or get more definition on the quilting. As of October 2023 we source our rolls exclusively from Quilter’s Dream. Here is a link to the Quilter’s Dream Wool website. It gives great information on the product including washing instructions.
*Be sure to view the website for full washing recommendations.
-
We are happy to accept your pieced backings. We fondly refer to them as ‘Frankenbattings’. Here are your secrets to success:
Be sure they are meeting our minimum requirements as pieced backings are more likely to be wonky, not square, and harder to manipulate. Those extra inches give us room to work with those potential issues. Also, be sure the pieces are secured together. A wide zig zag stitch and fusible tape are common methods.
-
Prewashing is mostly a personal preference though there are some standard recommendations out there in the world.
Quilt Top Fabrics: This is 100% a personal preference. We encourage you to do research around crinkle, shrinkage, color bleed, starch, and precuts in relation to prewashing.
Backing Fabrics: At TCQ we recommend that you treat your backing fabric the same way you treated the fabric in your quilt top to increase the likelihood that they will shrink at a similar rate during the washing process. However, there are some exceptions to this in regards to wide backs, flannels, and such. For more details visit the Backing Information page.
Batting: We do not prewash our batting, however you are certainly welcome to prewash your own before you send it our way. It’s best to read the instructions on the packaging or visit the manufacturer’s website of the batting of your choice to see what the washing recommendations are.
-
Doubling Up on Batting:
We occasionally get requests to double up on batting or use a combination of batting. If you know exactly what you want then I’m happy to do my best to accommodate you. If you are asking for my opinion or recommendation the first thing I’m going to do is ask what you are hoping to accomplish by doubling up. One of the only issues I caution folks against is two layers of high loft batting, such as wool, as it is almost too thick to go through my machine. It can cause issues with skipped stitches and pulled fabric on the quilt top especially if there are thick seams.Do I Need Batting?
Maybe not! The purpose of batting is to provide a layer of insulation and warmth to the typically thinner layers of cotton of a quilt. However, if you are not using your ‘quilt’ as an object to provide warmth, or if you are not using traditional quilting cotton, maybe you don’t need batting or maybe you can substitute something else. If you are using flannel for the top and/or backing fabrics then it’s common to use another layer of flannel in lieu of batting, or just skip the inner layer altogether. When a quilt has something extra soft, warm, or thick on the backing such as minky, microfiber blankets, or fleece, batting is not necessary for warmth, though some prefer to still use it for the extra weight and quilting definition. I’ve also quilted items meant to be used as tablecloths or light clothing where we skip batting to keep it thin and drapable. -
No Thanks! Occasionally, a quilter intends to quilt their quilt on their domestic machine and they spray baste their quilt sandwich. But then, life happens and they decide to send it to us. Excellent! However, all of that sticky basting spray is not great for the inner workings of my machines. We will use the quilt top, but we will require new batting and we will need to evaluate the backing fabric. If it’s fairly sticky we will ask for a replacement.
-
You are welcome to ask ‘what’s your current turnaround’ but my response will always be ‘we ask for 4 weeks in the studio unless you have a date in mind by which you need it returned.’ Everyone gets ASAP treatment though I do have a enough wiggle room to prioritize things when requested.
Here is that full formal answer:
We ask folks to allow for their quilt to be in the studio for 4 weeks. It’s rare that we need the full 4 weeks; our overall average turnaround is 2 ½ weeks. However, asking for 4 gives us a healthy cushion for all the services you might request and any planned or unplanned disturbances in the studio such as vacation or sick kiddos.
We are always willing to consider a faster turnaround if you have a particular deadline in mind. More often than not we can accommodate your request. Simply reach out and give us your hopeful return date and we can let you know if it’s possible and whether or not it will incur the $50 rush fee. The rush fee is rare, it only comes into play if we have to work outside of our usual parameters to meet your deadline, such as working through a weekend. We will always let you know ahead of time if this will be the case so you can decide how you would like to move forward.
-
While we guarantee a 4 week turnaround the bulk of the year, things do change around the holiday season. Here is our past year’s holiday season schedule, including TCQ’s winter break. While the exact dates change year to year, it’s important to be aware of those differences in our schedule.
-
We work hard to be as straight forward in our pricing as possible but we know it’s nice to have all that pricing in one place. With that in mind we are building a quilting calculator to help get an idea of what your costs may be. Coming soon!!
In the meantime, you are always welcome to reach out for an estimate.
-
Trace Creek Quilting is located in the heart of the USA - good ol’ STL, MO. (St. Louis, Missouri) This makes us convenient and relatively quick for shipping from all over the states.
If you are from the STL metro area, we are in South County, less than a mile from the intersection of 55, 270, and Lindbergh.
My home address, and where all quilts should be mailed/dropped off, is located on the order form that will accompany your quilts, along with all prep instructions.
-
At least 45% of our business is from folks who are mailing their quilts to us. Here are our thoughts on how to best get your quilt to us:
Mailing provider: Use whoever is most convenient and comfortable for you. You may save a few bucks by using one service over another but it’s tough to tell which provider that will be before packing it all up and swinging by their location. You’ll get it to us sooner by doing it the most convenient way for you. We do not have a preference and have not had more or less problems from any of the providers that service our neighborhood.
Packing up: Pack everything in a plastic bag that seals. A cardboard box alone will not protect your fabric items from water and/or other unexpected yuckiness that can creep into a box.
-
While we do our best to be responsive to text messages, FB messages, IG messages, etc… our official notifications will be via email. This allows us to easily reference conversations. However, if you have a quick question or are trying to arrange pickup/drop-off on short notice, text is best as I do not always see my emails throughout the day.
(tracecreekquilting@gmail.com, 314-374-5318)
Upon Arrival: Packages arrive throughout the day into our weatherproof drop box from all our delivery guys as well as the local folks who use our porch drop off. I usually collect whatever is out there 2-3 times a day and do one last check when we lock the doors at bedtime. Projects go into the studio to await opening and prep work.
We ask for 1-3 business days after your quilt is brought into the house for us to prep it and get back in touch with you to discuss any questions either of us may have. If your quilt arrives at my house on Wednesday, I’ll have it in the house by the end of the day. I then have Thursday - Monday to get in touch with you. I’ll admit, when both the studio and life are super busy I may not have time to fully prep your quilt within that time frame, but I work hard to at least reach out and let you know we have it so you do not worry.
This time frame allows me to open, prep, and organize in batches so I am the most efficient and focused with this task.
Upon Completion: Once your project is complete, we will send an invoice to the email provided on the order form. This email will have payment and mailing/pickup details for you. We usual invoice on Mondays unless it’s a holiday.
Local Folks: Once you have paid just let me know what day (M-F) you would like to retrieve your quilt from the drop box and I’ll have it out by 9am on that day.
Mail-In Folks: We print labels 2-3 times a week depending on how the fast or slow folks submit their payments. Your shipment will be in handled in the next batch after your payment comes through.
-
Check back to the Communication From TCQ tab just above this question.
-
Check back to the Communication From TCQ tab just above this question on how we will communicate with you once your project is complete.
Once your quilt is complete we will send an invoice to the email address listed on your order form. The invoice will have a link that will allow you to pay online. The system allows you to use your credit card, bank card, and PayPal. These are the only options for mail-in customers.
Local customers may also elect to pay via cash or check though there are some caveats. We do not allow quilts to be picked up before payment is made. To use cash or check you will need to make an appointment so I can meet you at the door. This can be tough as my hours are limited. If you pay online I can have your project on the porch by 9 am on the day (M-F) you wish to come by.
-
Yes, absolutely! You will need to let us know that you want extra insurance before a return label is printed, as well as how much you would like the packages to be insured for.
There are a few things to keep in mind; should you need to file a claim you will have to provide documentation that the value of the item matches the amount for which it was insured. Also, items insured over $500 sometimes require a signature upon delivery. (Based on Priority services through USPS). We use UPS and USPS so there are lots of nuances, but this is the gist of it should you be considering this option.
-
We LOVE to trim your quilts once we are done! It just feels so much closer to a finished project! The bulk of our customers opt into this service and it has become our default.
If you do not wish for us to trim your quilt, either so you can salvage every bit of extra backing fabric, or simply because you prefer that method, you can select ‘Do Not Trim My Quilt’ on the order form.
If we are trimming your quilt, we are simply removing the extra batting and backing fabric from the quilt top. Unless we are easing from one wonky point/extra fabric in the quilt to another, we do not cut into your quilt top.
It should also be clear we are not squaring your quilt. This often entails cutting into the quilt top or making judgement calls on what to trim which is not something we are keen on taking on.
-
When we load a quilt, we take many things into consideration, including how to return the most usable pieces of fabric back to you. When possible, we load a quilt off-center to push the extra fabric to 1-2 sides so the cuts returned are 1-2 bigger pieces rather than 4 smaller cuts.
However, there is a limit to what we will return as we have to think about the time and process it takes to trim up the little bits that remain after the quilt process. Strips smaller than 2-3” are not typically trimmed for return.
We respect that to our most scrappy conscious customers, that may be fabric you want. If so, we encourage you to select ‘Do Not Trim My Quilt’ on your order form so you can handle those bits in your preferred manner.
With all that being said, it should be noted that the 4” of extra backing fabric on all 4 sides of the quilt that we ask for should be thought of as a longarmer's seam allowance. Even if you don’t see it in the final product, it is a necessary part of the process that does get used up in various ways. We use it to baste down the batting, it gets quilted into as we run the quilting pattern off and back onto the quilt, and we sometimes use it as a tension testing ground when we start, stop, and change bobbins.
It should be your expectation, as it is ours, that this is our fabric to use as necessary to achieve the best results possible on your quilt top. There should be no expectation that this fabric will be usable after the longarming process nor will it be returned. If it works out, great! But let’s let that be a nice surprise rather than an expectation.
-
The widest our machines can handle is 120” of backing fabric, which means technically a 112” quilt top is our maximum quilt width. There are no limits in it’s length. Contact us if you have concerns or your quilt is right around these measurements.
We do have some size limitations on pantos that have long straight-ish lines such as Modern Curves and Straight Line Quilting. We only have one machine that can run these patterns and it’s max width is 90”. Be sure to check the panto description for these details.
-
Items with extra fabric in the borders, folds in the piecing, or unsquared backing (is that a word? Unsquared? Non-squared? Crooked?) may result in puckers or folds that get captured by the quilting. While we do our best to ease these out or go around them, it’s not always possible to avoid this.
-
TCQ no longer makes memory quilts or t-shirt quilts from scratch. If you are in STL you can try the Crafted in St. Louis Facebook groups. My personal recommendation is to look for someone who is highly recommended by their previous customers and who longarms their quilts. While these are not hard and fast rules, they indicate to me someone who is turning out professional quality products like we strived to do.
-
Do we quilt t-shirt quilts. Yes!! We are happy to do so with one major caveat: All of the knit fabrics in the quilt MUST BE STABILIZED. If not, the fabric will stretch under our needle creating folds, puckers, long stitches and/or skipped stitches. You don’t want that, I don’t want that, my machines really don’t want that.
-
We do not accept quilts that come from homes where someone smokes. It’s unfortunate, we do not intend to leave folks out, but we cannot expose other’s quilts and our studio to the smell they bring with them, however slight it may seem to the individual living in the home.
-
We are not pet free households, however we all work in areas that are closed off from our furry family members so your projects are never in direct contact with them.